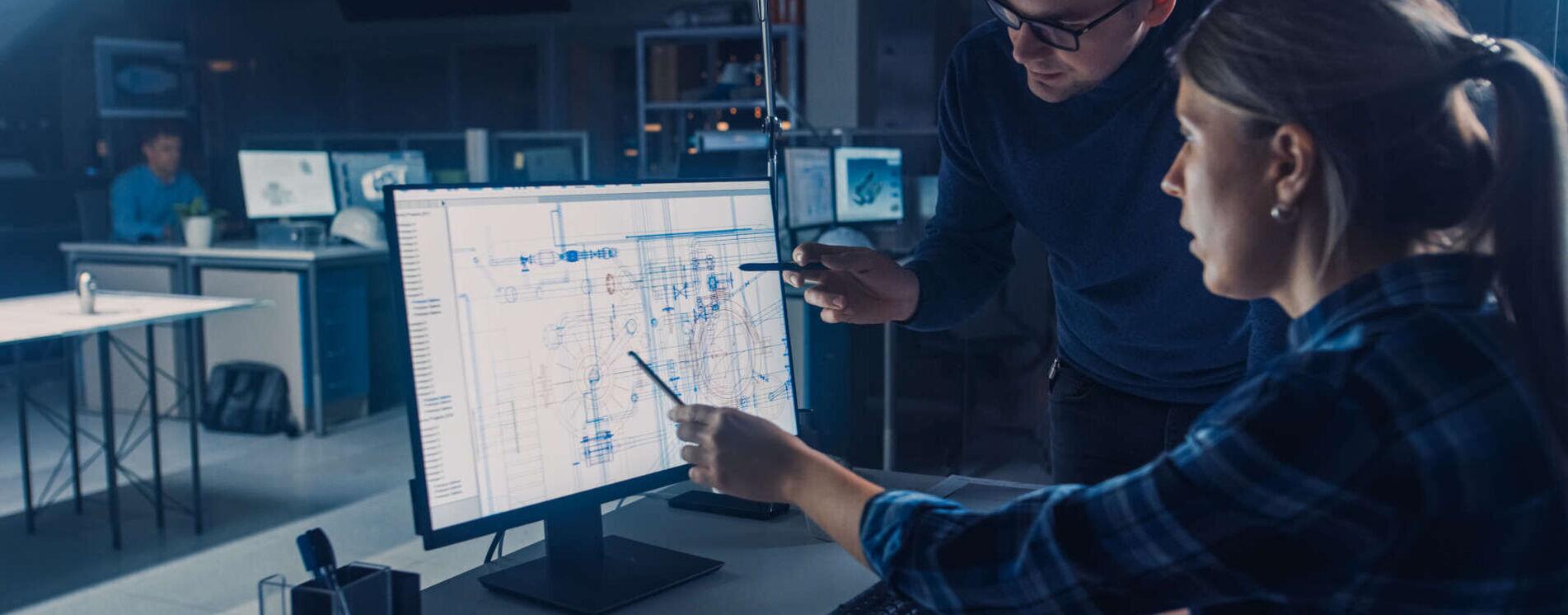
As we look back over the past decade from what is now a networked, intelligent and connected economy, we see the field of engineering as a transformed field. People used to equate engineering with the act of designing a product. Now it’s a means to a converged digital transformation in a connected enterprise and a way to stay relevant in a fast-changing market. Digital engineering has gone beyond the engineering department to enable new business models, deliver superior customer experiences and realize operational efficiencies.
We see this trend cutting across multiple industries. John Deere, the tractor company, has launched what is essentially a software business. Schindler and KONE have gone beyond elevator manufacturing to sell mobility solutions. Bosch no longer just makes appliances; it taps into IoT, monitoring and analytics tools. Verizon doesn’t just sell “network pipes” but offers additional services to enable a connected enterprise. A Tier-1 aerospace company no longer sells only landing gear or braking systems; it sells numbers of landings.
Engineering transformation: Engineering is not the same anymore
Engineering has changed in many ways. For instance, the cycle of delivery used to end with the point of sale. Now, the original equipment manufacturer (OEM) has to keep a product relevant for years through small, continuous releases that keep it aligned to consumer behavior. This has changed the way manufacturers think about sunset and capitalization by extending the life of the product. Over-the-air (OTA) updates are deployed not only by companies like Tesla. They are finding their way in the industrial industries to keep the equipment current and sustainable over years.
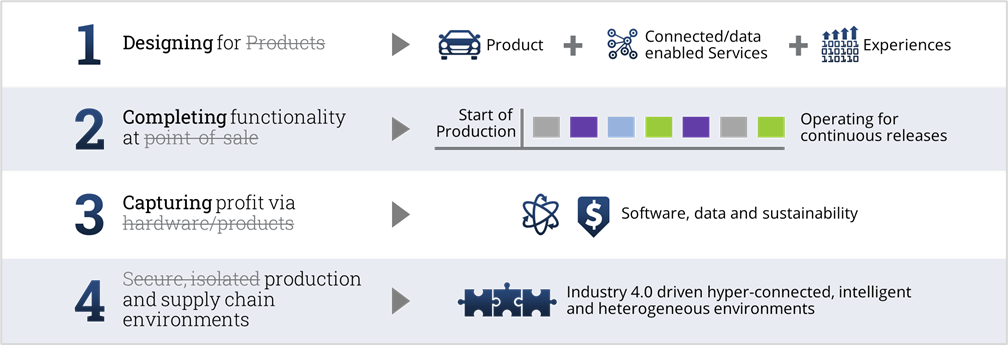
Also, the way businesses capture profits has changed. Selling hardware and products used to be the dominant way of realizing profit. Now, additional profit streams come from services, software and data insights that allow enterprises to get closer to their customers. Schindler still sells elevators, but insights from the use, maintenance and operations data can result in more revenue streams.
Engineering has become a means to a converged digital transformation across multiple domains of an enterprise.
COVID acts as a catalyst
The global pandemic hastened the digital engineering uptake. According to the 3Q 2021 Global ISG Index™, the annual contract value (ACV) for engineering services in the third quarter of 2021 rose 40 percent from the prior quarter and grew 300 percent from a year prior. Consolidation, another measure of a red-hot industry, has increased significantly. Six of the top 26 engineering firms have been acquired since 2019, and industrial companies have spent more than $20 billion on software- and engineering-related acquisitions in the past 18 months.
Organizations had already begun moving toward digital transformation when COVID hit and knocked supply chains offline. COVID acted as a catalyst towards a converged and a top-down, bottom-up approach to transformation. Use cases such as digital twins came down from PowerPoint slides and into reality as a way to ensure sustainability, resiliency and predictability of events and to make value chains more transparent.
Companies tried to bridge the gap between information technology (IT) and operational technology (OT) — essentially, between computers and industrial machinery — to be able to predict failure in their operations and find solutions that would enable remote access and thus remote maintenance and autonomous operations.
Similarly, enabling remote working was not limited to “office IT,” but enterprises needed to enable globally distributed product development that leverages remote/extended teams and virtualization and cloud technologies.
In this context, we see a few key megatrends emerging that will drive the engineering services industry over the next three to five years.
1. IT, OT, ET and CT converge for improving the odds of transformation success
Over the last few years, many companies faced the compulsion to “do a transformation,” most of which were driven in siloes, by either IT or OT leadership. This resulted in millions of dollars spent on transformation initiatives with few being scaled up or fully realizing the intended business value.
There is a clear realization now that digital engineering-led transformation must be looked at holistically across IT, OT, engineering technology (ET) and consumer technology (CT). To avert this disconnect, four levers come into play. They include: 1) realigned data, 2) a reimaged organization, 2) a redesigned ecosystem and 4) reshaped security.
- Realigned data means information flows across multiple domains of the connected enterprise and even beyond, within a connected ecosystem.
- A reimagined organization blurs the roles of COO, CIO, CDO and CTO, with a new split of responsibilities, know-how and reskilling across organizational domains. Those looser boundaries will blur ecosystem boundaries, too, to enable sell-to and sell-with opportunities.
- A redesigned ecosystem effectively manages the split between hardware and software responsibilities and flexible and modular contracts so multiple players can provide services.
- Reshaped security will address vulnerability to cyberattacks, especially in companies where OT is full of legacy systems. Organizations need a business continuity plan for critical functions and enterprise security alone will no longer suffice.
2. Industry 4.0 matures, augmented by digital twin/digital thread, IoT and edge computing
Industry 4.0 is maturing on multiple fronts. Companies are increasingly adopting digital twin and digital thread technologies to manage the “system lifecycle” and improve services revenue, supply chain traceability and connected product offerings. Traditional product lifecycle management (PLM) solutions were designed for a single company department working in isolation and are not efficient in extracting value from data that lies at the essence of Industry 4.0. Digital PLM, connected PLM, digital twins, and IoT solutions are combining networking, software, data and analytics to enable new use cases, such as improved asset utilization, enhanced asset performance, predictive maintenance and resilient and demand-driven supply chains.
While the cloud is a key enabler for these use cases, “cloud only” solutions may turn out to be expensive (e.g., network bandwidth and data storage options) or may fail to meet the latency and security/privacy requirements in some mission-critical cases. Connected systems are now no longer “cloud only” but necessitate optimization of cloud-edge as one continuum.
3. Software and data-driven capabilities become table stakes.
Enhanced customer experience, agility and new business models lie at the heart of the third megatrend. Software excellence and data insights allow the enterprises to tune their products, services and business models to customer needs. This has some fundamental repercussions. Companies will likely need to unbundle hardware, software and industrial DevOps and increase virtualization and cloudification, which will spur a dramatic shift in skills and talent. Talent acquisition and retention become big obstacles to transformation as enterprises increasingly take greater control of the software domains inhouse.
Managing the software development lifecycle also has some specific requirements, such as maintenance/management over long lifecycles and continuous development methodology. This calls for a revising the operating model toward a software and data-driven organization. The way businesses design, deliver, consume and partner to source will never be the same.
Given these three trends, what should organizations do next?
Mastering the new rules of the game for a networked, intelligent and connected economy include designing a new software operating model, optimizing a cloud-edge continuum and establishing digital twin/thread capabilities. Companies must manage quality and security “by design,” build resilient operations and supply chains, revitalize legacy applications and collaborate with the right ecosystem partners.